Recent developments in unmanned aerial vehicle (UAV) technologies has presented new, exciting opportunities for cost effective asset inspection and management in the power and utility industry.
PROJECT – Power poles are to be imaged with a UAV platform and any observed defects assessed, and reported in accordance with the Maintenance Standard for Overhead Pole Lines and Network Asset Defect/Condition Prioritisation standards.
Project Scope
- Data Collection
- Defect Analysis By Internal Linesman
- Deliver Defect Report
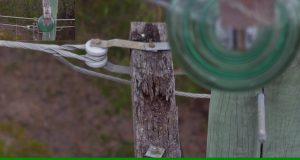
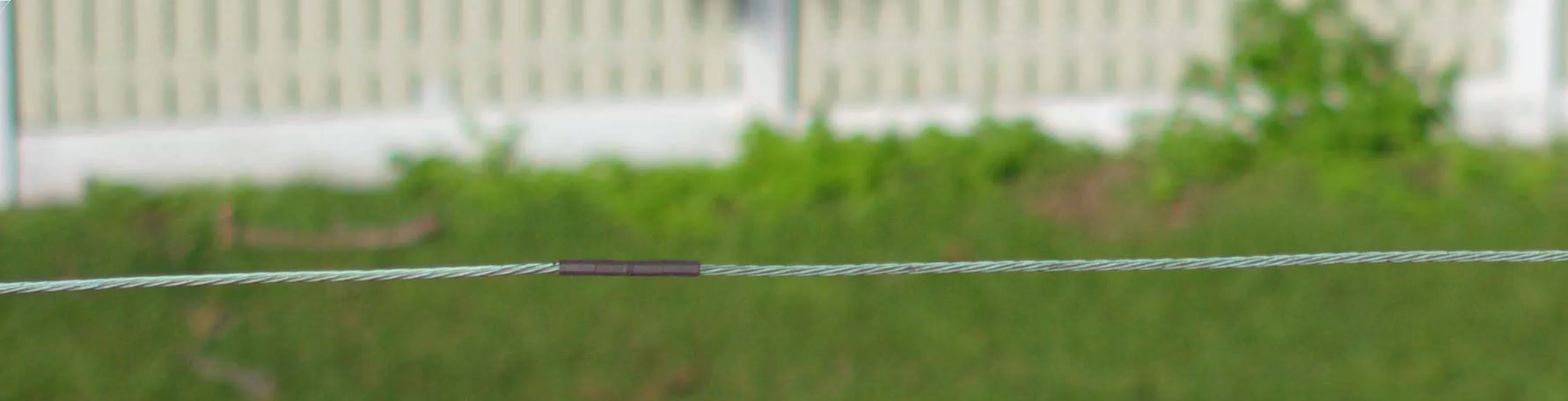
These works have two main components: Image acquisition; and image analysis (defects) and reporting including:
•Identify 11kV conductor type and condition.
•Inspect wooden power poles and cross arms.
•Identify anomalies such as gun shots, broken strands, third party damage, clashing, lightning or bird strikes etc.
•Identify 11kV conductor joint type and condition.
• Provide GIS locations of 11kV conductor joint and take photograph of each joint.
• Provide defect condition report of 11kV conductor and associated defect photos.
• Reporting included pole number check, photo of the pole with this site number clearly shown; reference of the photograph(s) to associate to the pole number; raising a defect if the number is incorrect / damaged / missing etc.
METHODOLOGY
Images to show the road where possible, to detail which side of the pole the defect is on such as footpath side or road side or some other indication as to the side of the pole shown.
Images were taken form a vertical perspective of the pole top, from the offset view being perpendicular to the line on a horizontal plane and from 45 degrees at a height of 5m above the pole; from these angles inspection is possible for all almost defects of the pole top.
Systemic inspection begun with the inspection of the cross-arm for deterioration / rotting, splitting, burns / fungal attack or corona deterioration causing the hole for the pin insulators to enlarge and the hole size to increase. It then continued to the insulator to inspect the conductor ties for any corrosion / breakage of the tie and any damage to the conductor from the broken / corroded tie. Insulators were inspected for any fractures, cracks, chips or other discolouration which may indicate flashovers. Where possible the hardware including bolts, cross-arm straps were assessed for tightness by inspecting the volute washer for its size / looking for air gaps between components.
Pole caps were inspected to ensure they were secure and not corroded through causing pole top deterioration. Any strain / termination strings were inspected for corrosion of the fittings at the joints and between the discs, the preformed / compression deadens inspected for any signs of slippage or fatigue. Stain eyebolts were inspected for indication of pulling through the cross-arm or that the eyebolt had vibrated loose.
Stays were inspected for any movement of the eyebolt through the pole and any corrosion on the stay fittings or wire; including where possible the inspection of the stay insulator for any damage. All bolts under tension were inspected for ‘pulling’ through the wood, as this is an indication that the wood has internal rot and is deteriorated.
“Asset inspections and audits were conducted on 5000 wood and concrete power poles. We then assisted in the development of the Asset Inspection Defect Management (AIDM) work procedures for our energy client.``

OUTCOMES AND BENEFITS
•Successful completion of the alternative technology trial saw the following Client benefits:
•Reduced OHS / WHS inspection risks.
•Reduced costs associated with hire and setup of elevated work platforms and harnesses.
•Reduced interruptions to electricity supply.
•Optimised allocation of resources for proactive issue investigation and resolution, instead of time-consuming reactive work.
• Early detection of maintenance issues leading to time and cost savings.
• More efficient maintenance planning through efficient defect reporting.
• Improved asset register accuracy and completeness, verified by high resolution imagery and geo-location precision.
• Enhanced data / reporting and image availability for stakeholders.